Adherence to quality requirements for plastic components in MedTech is becoming increasingly important as MDR and IVDR dictate more stringent regulations for consumables. The quality control and shelf life aspects present significant challenges, and so dimensions and tolerances play a crucial role in the smooth manufacture, reliable safety, and accurate functionality of a component.
In our topical article below, our Operations consultants share their knowledge on the dimensional changes of injection moulded consumables from manufacture to the end of shelf life, as well as some advice for achieving efficient adherence to the necessary quality requirements.
The difference between plastics and metals
To understand the dimensional changes of injection moulded consumables, it’s important to firstly note how plastics differ from metals. Plastics are divided into three categories:
- Elastomers
- Thermosets
- Thermoplastics
Elastomers
Elastomers are polymers that are held together by weak intermolecular forces. They are viscous as well as elastic, which allows them to deform or stretch under extreme tensile and compressive loads, before returning to their original shape.
Thermosets
Thermosets retain their condition and shape after curing due to spatial crosslinking. Once cured, their polymers can no longer be dissolved.
Thermoplastics (amorphous / semi-crystalline) & Thermoplastic elastomers
Thermoplastics become pliable at elevated temperatures but become less so once cooled. They can withstand very high temperatures, so the heat required for melt processing must be higher still. Unlike thermosets, thermoplastic materials can be moulded as often as is desired by cooling and reheating, as long as the material is not overheated – as overheating causes the material to degrade. Thermoplastic elastomers possess both thermoplastic and elastomeric properties. For high volume medical devices, thermoplastics are generally used during injection moulding processes due to better processability.
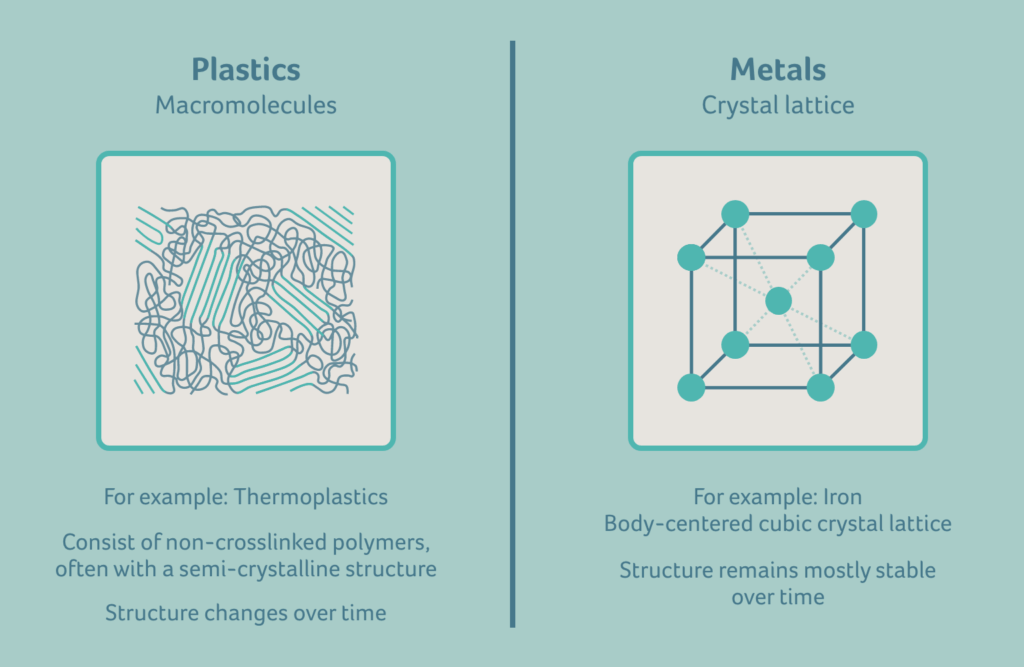
The injection moulding process
The injection moulding process involves the heating of a thermoplastic polymer to above its melting point, resulting in the conversion of the solid polymer into a molten fluid with a reasonably low viscosity.
The melting is mechanically forced – i.e., injected, into a mould shaped like the desired final object. The low viscosity of the molten polymer allows the mould to be completely filled. The article resides in the mould until it is cooled below the freezing point of the polymer.
When dealing with semicrystalline polymers, the crystallinity of the object (which governs its appearance and mechanical properties), is usually controlled by in-mould cooling of the object at a defined cooling rate.
The last step involves opening the mould to eject and recover the part.
Dimensional changes from manufacturing to end of shelf life
The overall shrinkage of a component is comprised of moulding shrinkage and post-shrinkage.
According to ISO 20457:2018, the moulding shrinkage is:
“the relative difference between the tool contour dimension at 23°C ± 2 K and the corresponding moulded part dimensions 16h to 24h after production, stored until measurement and measured according to ISO 291:2008, unless otherwise specified by contract or the relevant ISO-material specification.”
ISO 294-4:2018 defines post-shrinkage as:
“the dimensional difference of a moulded test piece, between the beginning and the end of a post-treatment, determined at room temperature.”
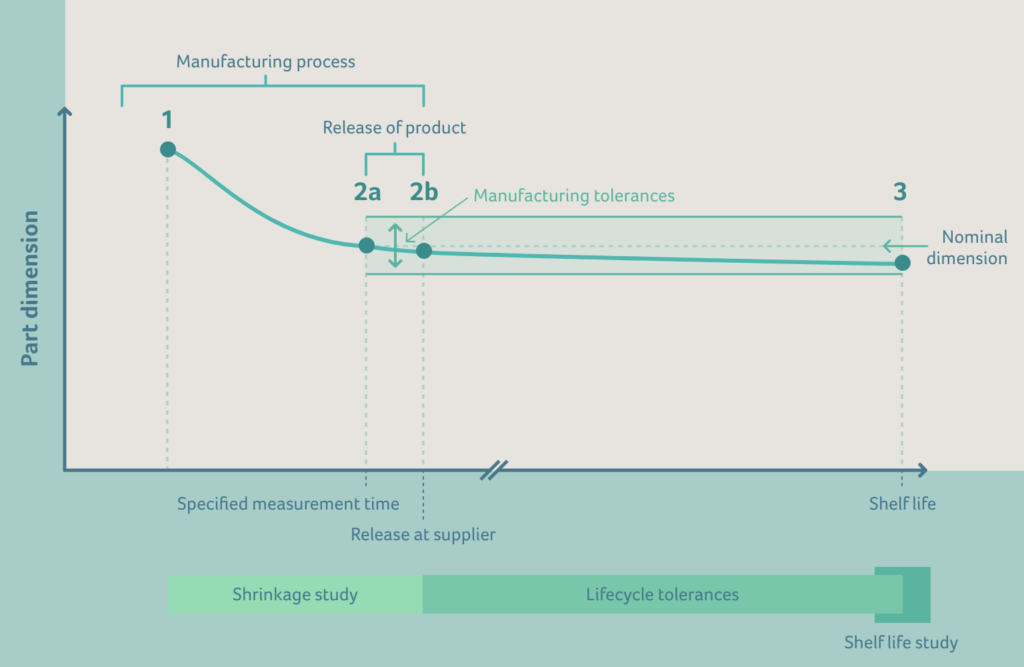
The diagram above can be explained as follows:
1 – 2a | Shrinkage after demoulding by cooling and shrinkage due to crystallization
Moulding shrinkage results from the volume contraction that a solidified moulding material experiences in the closed mould cavity. Due to the compressibility of the polymer, it contracts, however, this volume contraction is not a constant variable. The resultant contraction also depends on the pressure inside the mould.
Crystallization takes place during cooling. Partially crystalline polymers undergo a transformation from an amorphous liquid phase to a partially crystalline solid phase. If the plastic falls below the crystallization temperature, then linear or only slightly branched chains with easy-to-align repeat units will reconfigure themselves into an ordered (crystalline) state with a lower free enthalpy. The polymer chains lie parallel to one another, tightly packed in some cases, forming fine crystallites in which almost complete order prevails, except for a few defect points.
To understand how the dimensions of manufactured parts change over time, it’s advisable to perform shrinkage studies. These studies need to be performed to calculate tool dimensions which are required for passing the First Article Inspection (FAI) as described in ISO 13845.
2b – 3 | Shrinkage by aging
Temperature and humidity changes lead to a dimensional change of any physical part. This effect is known as thermal expansion and contraction. Aging of the material may lead to a permanent dimensional change in the plastic part, for example due to secondary crystallization and relaxation effects.
As outlined in ISO 20457:2018, dimensional changes are the result of:
- Molecular short-range order effects e.g., post-crystallization readjustment of molecular orientations
- Chemical reactions e.g., post curing
- Dissipation of volatile components or drying out e.g., water, condensation products, solvents, thinners, plasticisers
- Migration of liquid and solid components e.g., plasticiser migration, chalking
- Relaxation of elastic tensions
The lifecycle tolerance (dimension range analysis) is a tool that can be used to estimate the variation of the critical dimensions during the whole lifecycle of the consumable based on expert knowledge. With the calculated tolerances, consumable-instrument interfaces can be designed in such a way that both newly manufactured and aged consumables fulfil their function in the system safely and reliably.
3 | End of shelf life
The shelf life of a consumable is the duration for which the consumable maintains its functionality and usability under the storage conditions specified by the manufacturer. The claimed shelf life of a consumable is valid within a certain temperature range, which is displayed on its label.
For CE/IVD labelled consumables, a shelf life needs to be specified on the label by an expiry date. Under the IVDR, a shelf life study is mandatory to support this claim and needs to be documented accordingly.
Shelf life studies evaluate accelerated and real-time aging. Whilst requirements and guidelines on the procedure to be used for accelerated aging methods are not defined by the IVDR, the ASTM Standard F1980 proves a useful resource on the topic.
The initial shelf life claim at market introduction is generally based on the data from the accelerated aging studies as part of design verification. Bear in mind though, that it is possible to plan the accelerated aging study to reach beyond the launch of the consumable, so that the initial shelf life claim at market introduction can be subsequently extended.
5 tips to take away
Define and integrate specifications for manufacturing tolerances as well as for the product’s lifecycle to ensure adherence to quality requirements.
Get a deep understanding of your material properties over their lifetime to avoid deviations and field complaints. Whilst you can find some information on materials within their corresponding data sheets, it is the nuances of the moulding process that influence the material behaviour over time – so look to your toolmaker and moulder as sources of knowledge on this.
Optimise the repeatability and reproducibility of your processes for a more efficient production environment. One way of achieving this is by completing process design studies to identify attributes that contribute the most variation, and then focusing controls to monitor these attributes.
Define the time points at which you will test the functionality of certain specifications when you plan your aging study. Whilst your Notified Body will mainly focus on your final time point, it’s important to understand your product’s behaviour throughout its lifecycle to accurately identify any potential problems. You should try to maintain a balance with the amount of time points defined however – too many, and you will waste materials, effort, cost, and resource, but too few, and you risk losing time point accuracy if there’s an issue.
Closely collaborate with your suppliers during product development and manufacturing to ensure you share the same set of process requirements, and that there’s a robust shared consideration of the dimensional changes throughout production and product lifecycle.
Should you have a challenge related to the dimensional stability of consumables, or process engineering more generally, our Operations team is ready and happy to help. Simply get in touch to start the conversation.
Further Reading